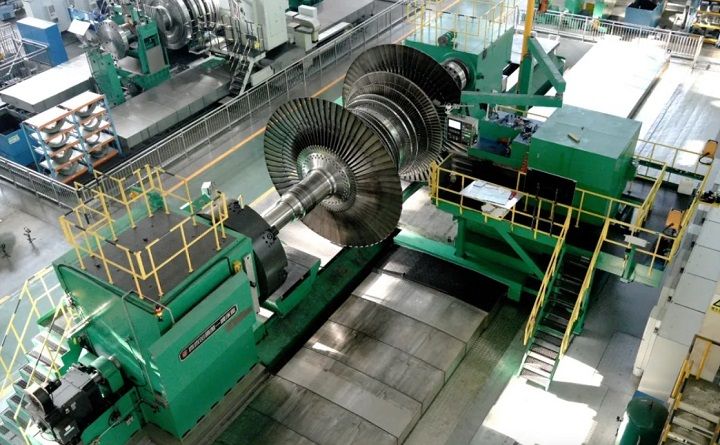
汽轮机作为重要的动力设备,其技术进步和市场表现对新质生产力的发展有着重要影响。近年来,随着汽轮机市场需求的增长,对其核心部件汽轮机转子的精度要求越来越高。然而,国内核电大型汽轮机转子“外窄内宽”凹槽的加工,一直是限制国内汽轮机产出速度主要因素。在传统加工“外窄内宽凹槽”时,需要进行12次手动换刀再对刀才能完成加工,加工效率低,且主要核心技术加工精度无法达标,长期受制于人。
而国内技术的不断发展,使得这一局面逐渐被打破。12月12日,齐重数控装备股份有限公司为哈尔滨汽轮机厂有限责任公司研制的重型数控卧式车床在设备安装现场举行交付仪式。产品攻破了我国加工大型汽轮机转子设备无法达到精度指标的技术难题,解决了高精加工设备“卡脖子”问题,为实现汽轮机转子核心加工设备国产化提供了重要保障。
记者了解到,此台重型数控卧式车床是专为核电大型汽轮机转子等高精度零件加工的国产化设备,能够完全达到关键技术指标要求,是具有更高效,高精度、高刚性、高可靠性的自主知识产权产品。机床最大车削直径4.5米、最大工件长度16米、最大工件重量350吨、主轴端/径向跳动达到0.005mm。
值得注意的是,为解决“外窄内宽”凹槽的加工难题,项目团队攻破了全自动摆角刀板技术,使刀板在小于60mm的狭小空间内,实现布置出传动、分度、锁紧功能的机构,并且在此基础上完全能够进行切削加工,将加工效率提高3-4倍,此项技术在同规格加工设备中为国内首创。
此外,汽轮机转子尺寸及精度要求极其严格,尤其是工件跳动精度的稳定性,直接影响汽轮机转子的可靠性。为攻破这一难题,研发人员从利用虚拟机床技术模拟分析齿圈受力状态、改进主轴支撑结构,到优化加工工艺、严格把控基础零件精度、创新装配工艺,最终实现了现场实测机床主轴端径跳0.005mm,完全满足转子加工需求。本产品同样适用于重型轴类及其它回转类零件,如大型电机轴、发电机轴、电机转子等零件的外圆面、圆锥面、端面、切槽、螺纹及回转曲面的车削加工。
来源:中国工业新闻网