增材制造技术(俗称 3D 打印技术)是制造下一代更有可持续性的燃气轮机&航空发动机的关键技术。增材制造工艺最大程度地提高了设计灵活性,并能集成额外的功能,对于复杂轮廓的设计优化也无额外的成本,这使得部件的设计不再局限于传统技术的约束,从而为复杂燃气轮机&航空发动机零部件创新与优化带来了更大的空间。
增材制造技术最早起源于美国。20 世纪 80 年代后期,随着计算机技术的进步,增材制造技术有了根本性的发展。增材制造技术的突出优点是可不借助机械加⼯或模具,直接⽤计算机三维设计的图形数据制造出形状复杂的零件,⼤⼤缩短了产品的研发周期,提⾼了⽣产效率且降低了⽣产成本。
谈到增材制造技术估计很多人并不陌生,但是说到增材制造技术的应用,可能大部分人还只停在以下两个阶段:
1.原型制造
即通过树脂、塑料等非金属材料打印的概念原型与功能原型。其中概念原型用于展示产品设计的整体概念、立体形态和布局安排,功能原型则用于优化产品的设计,促进新产品的开发,如检查产品的结构设计,模拟装配、装配干涉检验等。
2.间接制造
即通过 3D 打印技术完成工、模具制造,再采用3D 打印工模具进行零件的制造。殊不知,伴随着 3D 打印技术的发展,特别是金属 3D 打印技术近年来取得的进展,增材制造技术的应用已不仅仅局限于快速响应产品的外观设计,抑或是工艺辅助的间接制造,而是延伸到了金属功能零件的直接制造。
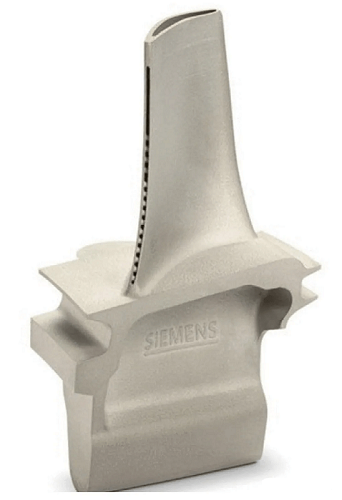
当前,通过金属增材制造技术制造的金属材料零部件越来越多的被成功应用于航空航天,国防军工、医疗器械、汽车制造、注塑模具等领域。
可以说,金属增材制造技术在制造行业具有更广阔的应用舞台,是增材制造领域对制造业来说最有应用价值的先进制造技术。主要体现在以下几个方面:
1.制备高成本材料零件
金属材料是制造领域必不可少的重要材料,但是在实际的加工过程中,却存在着不少问题,例如钛合金、高温合金、超高强度钢等材料难加工、加工成本高、材料利用率低,加工周期长等。
金属增材制造技术所采用的激光、电子等高能束密度高,速度快,极大地改善了金属材料的加工难度,并提高了材料利用率及降低了原材料成本。
以金属增材制造技术应用最早和最广泛的航空航天行业为例。航空航天基于高性能需求,需要大量使用钛合金和镍基超合金等昂贵的高性能、难加工的金属材料。但零件的材料利用率非常低,一般低于 10%,有时甚至于仅为 2%-5%,大量昂贵的金属材料变成了难以再利用的废屑。
美国最大的航空发动机制造公司之一普惠公司应用增材制造技术用于发动机的镍基合金和钛合金部件的研制,结果显示:不但获得了与当前材料一致的性能,大大缩短了制造周期,提升了复杂几何结构的制造精度;而且原材料消耗降低了 50%,并将发动机的 BTF 比(原材料质量与部件最终质量之比)从传统工艺的 20:1 降低到 2:1 以下,有效地提高了部件的质量和降低了制造成本。
2.高性能成形修复受损零件
高成本零件的成形修复也是金属增材制造技术的突出优势。
过去,对于受损零部件只能做表面的涂层修复,并且维修工序步骤繁多,还涉及一些额外的步骤如加工、抛光、测试等,同时还受维修时限条件的制约,耗时较长;而对于损伤稍严重的零部件也只能作更换处理。金属增材制造技术则可以对任意缺失或损坏的部分进行快速成形和修复。
例如航空航天零件结构复杂、成本高昂,一旦出现瑕疵或缺损,只能整体换掉,可能造成数十万、上百万元损失。而通过金属 3D 打印技术,可以用同一材料将缺损部位修补成完整形状,修复后的性能不受影响,大大延长了使用寿命,降低了成本,减少了停机时间。
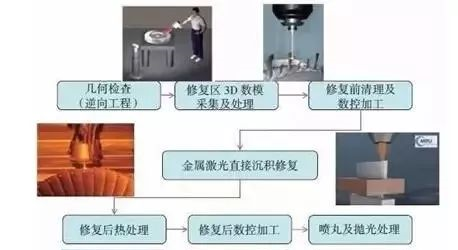
其实除了航空航天领域外,机械、能源、船舶、模具等行业也对大型装备的高性能快速修复提出了迫切需求。
据悉,西门子公司计划从 2014 年开始采用金属 3D 打印技术制造和修复燃气轮机的某些金属零部件,并称在某些情况下,通过 3D 打印技术可以把对涡轮燃烧器的修理时间从 44 周缩减为 4 周。
异质材料的组合制造
对于传统制造方式(铸造、锻造等)来讲,将不同材料组合成单一产品非常困难,但是增材制造技术有能力使不同原材料进行组合制造。
金属增材制造 LSF 技术可以在通过铸造、锻造和机械加工等传统技术制造出来的零件上任意添加同/异质材料的精细结构,并且使其具有与整体制造相当的力学性能。
因此,针对部分工业零件适当利用增材制造技术进行组合制造,不同的结构部位采用不同类别的金属材料,不仅大大提高结构件的性能,而且降低了成本,特别是昂贵材料的成本。同时,也把增材制造技术成型复杂精细结构的优势与传统制造技术高精度的优势结合起来,形成了最佳的制造策略。
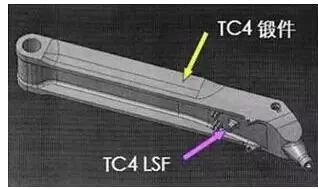
结合拓扑优化的轻量化制造
增材制造技术快速自由成型的特点,给产品的设计带来了无限的创新空间,为实现最优化的设计提供了有效的制造途径。特别是当前应用得比较多的拓扑优化技术,与传统的经验式设计模式不同,经过拓扑优化的创新模型是在满足设计约束下的最优拓扑结构。
但是优化后创新模型结构十分复杂,可制造性差,因此在设计阶段不得不引入制造性约束,以满足传统加工制造工艺的要求。往往这样得到的产品结构是牺牲掉了其在轻量化和高性能上的优势。而金属增材制造技术则可以使这些经拓扑优化后的创新模型,不用考虑制造约束并快速实现制造。
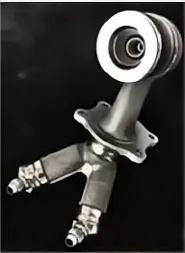
例如,空客 A320 飞机的大尺寸“仿生”机舱隔离结构,这一结构是通过拓扑优化设计,金属 3D 打印制造而成,材料是采用的超强且轻质合金材料 Scalmalloy。A320 全新的机舱设计与原有的隔离结构相比,新型的仿生隔离结构由几个不同的部件组成,不仅强度更高,而且将其总量减轻了 45%。
另外,GE 采用增材制造技术制造的 Leap 喷气发动机的金属燃料喷嘴,是通过长达 10 多年的探索通过不断优化、测试、再优化,才达到零件数量从 20 多个减少到了一个。
这样造出的燃油喷嘴不仅重量更轻,而且改善了喷油嘴容易过热和积碳的问题,将喷油嘴的使用寿命提高了 5 倍;另外,减少组装也提升了喷嘴的稳定性,并为公司降低了物流、组装、焊接等方面的成本。
成形传统工艺制造难度大的零件
在制造领域,有些零部件形状复杂、制备周期长,应用传统铸造锻造工艺生产不出来或损耗较大。而金属增材制造技术则可以快速制造出满足要求的零部件,并具有加工周期短、制造成本低、无需工装和模具等优势。
一个典型的应用就是模具行业随形冷却金属模具的制造。
金属模具冷却系统是设计模具工程之一,传统的模具冷却系统是以直线的水路设计为主,制作较简易,但需要的散热时间较长,直接影响了脱模时间、制品质量、制品外观等。设计者通过软件分析模具与水路的散热情形,设计出了异型水路,但是受到既有加工技术的限制,使得异型水路设计只能停留在理论阶段。
快速成形小批量非标件
增材制造技术非常适合个性化定制生产、小批量生产。
当前,金属增材制造的个性化制造在医疗器械的应用极为突出,例如用于打印具有个性化需求的植入物/假体或模仿仿生原理的复杂结构。
个性化、小批量生产已经成为当前制造业发展的趋势,金属 3D 打印摆脱了模具制造这一关键技术环节,可以随时调整参数,以更低的成本更短的周期进行小批量甚至单件产品的生产。除了医疗器械行业,在其他行业也极具应用潜力。
增材制造技术改变了传统的制造方式,为复杂金属结构功能件的直接制造提供了新思路,对于制造业而言有着广阔的应用前景。未来金属 3D 打印机将会越来越多的取代部分传统加工制造设备,但是增材制造技术也有其缺陷与不足,并不能完全取代减材制造,而是并列互补的关系。
来源:航空发动机人