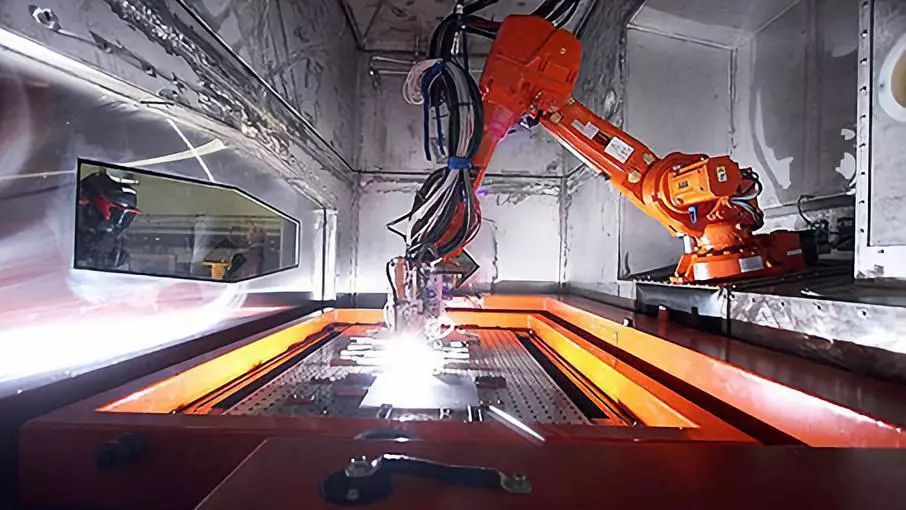
增材制造不再仅仅用于原型件制作,越来越多的技术被用于制造可投入生产的零件,这迫使工程师开始考虑联合的设计和组装过程。装配杂志给我们带来了一些专业人士的看法。
许多打印的组件最终需要与其他零件或组件连接,而且,某些零件太大而无法在单个3D打印机上生产。无论是金属还是塑料,都可以通过传统的三种连接工艺来组装打印的零件:粘合剂粘合、机械紧固和焊接。通常,大多数塑料零件是用粘合剂连接的,而许多金属零件是用螺钉和其他类型的紧固件组装的。
增材制造通过将一层材料沉积在另一层材料上来“打印”数字文件中的实体对象,而不是从经过切割和模塑实体材料开始。该技术使公司可以更轻松地制造用传统减法制造方法难以制造的复杂形状和结构。此外,浪费也更少,从而缩短了安装时间并降低了材料成本。塑料零件通常使用紫外线、红外线或可见光结合激光或热能量制成。金属零件是使用以金属粉末为原料的基于激光或电子束的打印机生产的,激光或电子束将粉末熔化在一起。
增材制造的好处之一是零件整合。以前需要组装的复杂、多组件零件可以作为单个对象进行打印,这使工程师能够将多个零件或组件整合为一个零件,从而节省了时间和组装成本。增材制造的长期目标是简化或减少组装需求。实际上,许多塑料打印零件都采用卡扣配合,从而完全不需要粘合剂或紧固件。通常,卡扣配合保持在模具制造的几何约束之内,并利用塑料的能力进行弹性变形,然后通过卡扣成形。
菲利普斯螺钉公司总裁迈克·莫温斯(Mike Mowins)表示:“当前采用增材制造技术的驱动因素之一是高完成度的成品零件,它通常省去了多个组件,或优化了需加工零件或零件组的设计结构。与传统的机加或模制零件相比,通过增材制造生产的金属或塑料零件重量轻得多,并且几何形状更复杂。结果是,你会有一个单个的零件,它仍然会使用与最初设计的零件相同的紧固件,但零件但会更轻,并具有优化的结构几何形状。”
随着越来越多的制造商开始打印可用于生产的金属和塑料零件,他们迟早需要将这些零件连接到采用传统制造技术(例如模铸,注塑或机械加工)制成的其他组件或零件。
一、航空航天应用
航空工业一直处于在生产中采用打印零件的最前沿,这些零件可用于从商用飞机座舱到喷气发动机的各种应用。打印的零件(例如支架)通常连接到铝或碳纤维复合材料组件。例如,空中客车公司的工程师最近将3D打印的钛合金支架连接到了A350 XWB客机的铝制挂架上。其它主要的航空航天制造商,例如波音,通用电气和洛克希德·马丁公司,也都对该技术持乐观态度。
波音公司卫星系统高级技术研究员理查德·阿斯顿(Richard Aston)表示:“我们已经不止于卫星和载人的航天器,并将该技术应用于导弹、直升机和飞机。随着增材制造成为主流制造方法,通过设计为一个集成的机械系统,可以显著提高可制造性并降低成本。但是,如果没有足够的理解并将整个系统作为一个整体重新设计,就不可能优化增材组件。”
莫温斯表示:“大多数航空航天增材制造应用涉及几何形状最优化的金属零件,而传统的加工技术是无法实现的。最终的零件仍具有与传统机加零件相同的功能,实际上,它通常具有与原始零件相同的尺寸范围,并且在连接界面处使用与原始零件相同的紧固件。在优化打印零件的同时,还有优化紧固件的巨大机遇。如果工程师采用最新的增材制造技术,那么也应采用最新的高性能紧固件。”
莫温斯指出:“这是我们看到公司Mortorq螺旋驱动凹入式紧固件和Mortorq超级外置螺栓应用最多的地方。航空工程师正在用这些重量更轻的新型零件代替传统的紧固件,这些零件可提供更大的扭矩控制和强度。当然,大多数增材制造活动仍在研发层面,你可以通过3D打印快速生产多零件组装的原型件,然后使用手工模型对设计和组装工艺进行分析优化。我们与罗·罗和其它公司进行了此类练习,提供了3D打印的零件以配合其结构的重新设计,并实时进行了零件组装的优化。”
随着增材制造技术的成熟,材料的性能正在大大提高。这为连接打印零件创造了新的机会。汉高公司3D打印技术客户服务经理盖德·麦古克(Ged McGurk)说:“在大规模定制可获益的行业中,我们看到了更多的应用,例如体育用品或医疗设备。还有很多应用是小批量制造工作,例如航空航天和专用工业机械。”为了应对这些应用,汉高一直在为各种增材制造技术开发先进的粘合剂,例如用于熔融沉积成型(FDM)的专用长丝和用于基于熔融系统的粉末。
麦古克表示:“就像任何需要集成到最终组装件中的工程组件一样,如果工程师对增材制造工艺的能力和局限性有充分的理解,那么连接打印零件就会相对简单。不同的打印技术将生产出具有完全不同特性的成品,即使是打印相同的3D模型也是如此。最终零件的尺寸精度和稳定性,以及表面光洁度和某些机械性能的各向异性都会对最终组装操作产生影响。在这些情况下,可能需要进行设计更改以生产针对整个制造周期进行优化的零件。”
EWI结构完整性首席工程师威廉·莫尔(William Mohr)补充道:“连接打印零件是一个活跃的研究领域,难度可能会有所不同,具体取决于所打印的材料和你尝试将其连接的材料。但是,对于金属和塑料零件,最常见的材料选择很容易焊接到相似的材料上。”莫尔认为,异种材料的连接更具挑战性。“总的来说,用于增材制造的合金是可焊接的,即使是用于不同的连接。关注的领域可能是变形、材料性能、性能下降和腐蚀。变形是由于,直接来自增材工艺的零件通常已经具有高张力的残余表面应力,该残余应力会在连接过程中通过加热而改变。由于增材材料可能具有产生自沉积的微观结构定向效应,从而导致材料性能下降。”
二、性能变量
打印零件具有工程师应仔细考虑的不同属性和性能特性,例如弹性、孔隙率和刚度。例如,通常不同材料的腐蚀风险预期更高。但是,增材制造的材料在化学上往往会发生局部细微变化,从而加剧腐蚀效果。
麦古克表示:“与使用注射成型等传统方法制造的相同零件相比,即使使用相同的基本聚合物或金属,打印零件的物理和机械性能也可能有很大差异。从材料科学的角度来看,这不足为奇。例如,最古老、最常见的工程材料之一——碳素钢,可以通过回火或退火来改变其内部结构,从而产生截然不同的性能,3D打印也是如此。”
麦古克指出:“在这种情况下,打印工艺产生的逐层结构创造出本质上会各向异性的特性。层状结构还会导致结构中的缝隙或空腔,从而导致孔隙出现。这种孔隙度会影响零件密封或容纳流体的能力。分层结构在打印件的表面光洁度或粗糙度上也很明显。工程师必须在打印过程中控制零件的方向,因为这最终将决定成品组装件的承重性能。表面属性(孔隙度或粗糙度轮廓)的变化也可能对粘合剂分配或组装过程产生影响。”
EWI的莫尔表示:“在许多情况下,你试图使用增材制造来达到与铸造、锻造或机加零件相同的设计标准,因此将这些差异降至最低。有时,你可以利用工艺的灵活性来减少总重,同时仍然满足设计意图。这在减轻重量直接关系到燃料成本的航空航天应用中将是非常有益的。构型的优化将增加使用中材料的平均‘活性水平’,对于更敏感的材料,这在材料的弹性行为中可能是显而易见的。”
莫尔说:“打印零件中的孔隙度对组装过程的影响与铸造过程中的孔隙度相似,不同之处在于,打印零件的孔隙率分布往往比铸件更均匀。对于在连接界面处需要气密密封的情况,对均匀性的预期有助于其设计,因为孔的局部组合不太可能是几近穿壁的。连接方法的类型必须与打印零件的设计和后处理相关联。例如,与钎焊到一个组装件上相比,打印零件上的套筒接头将需要不同数量的准备工作,因为钎焊需要更光滑的表面。在许多情况下,无论在任何情况下都需要对打印零件的一面朝向基板进行准备,这为解决后续组装过程的特殊需求提供了一个地方。”
三、连接替代品
粘合剂、紧固件和焊接都可用于连接金属或塑料印刷件。莫温斯表示:“我们仍然看到相同类型的连接技术正在使用。用于传统模塑塑料零件的螺纹成形紧固件与打印塑料零件之间没有太大区别。具有激进的螺纹轮廓的紧固件将提供与任何一种零件的良好连接。”
Stratasys的首席应用工程师艾伦·克雷默(Allen Kreemer)表示:“连接技术没有改变,任何常规的连接方法,例如粘合剂粘结或机械紧固都可以使用。例如,采用FDM技术打印的零件可以与多种类型的环氧树脂和氰基丙烯酸酯粘合。我们还测试了有机硅、聚氨酯和紫外线固化胶粘剂。二元的环氧树脂通常用于粘合FDM部件,使用后,在环氧树脂固化的同时将粘合部分固定或夹紧。氰基丙烯酸酯的拉伸强度高于环氧胶粘剂,但是,它对高温、化学药品和溶剂的抵抗力很差。因此,与氰基丙烯酸酯的粘合可能会降低FDM零件的性能。因此,建议将其用于概念模型和形状配合的原型,而不是功能原型或制造的零件。”
超声焊是另一种连接方式,特别是对于用热塑性材料打印的零件。克雷默表示:“当需要更高的强度时,可以将超声焊与其它方法结合使用,这种方法对于大块头或笨拙的组装件特别有用。机械紧固件是另一种有效的选择。“连接FDM零件时,可以使用大量的机械紧固方法和硬件选择。机械连接零件的一种独特方法是在零件的制造过程中将紧固硬件插入零件,当它从打印机中出来时,紧固件就被集成到零件中。”
来源:民机战略观察