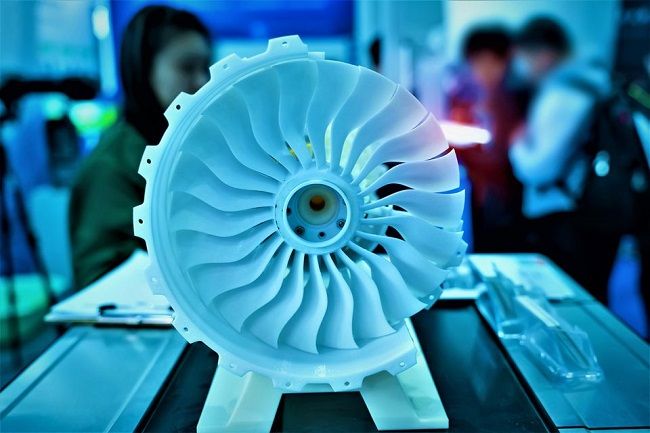
金属3D打印在航天领域获得广泛应用,特别是发动机领域,但还处于起步阶段。3D打印的特点:一是降低成本,材料利用率提高。二是缩短周期,3D打印在产品研制过程中不需要专用模具,导致研制周期缩短。三是快速迭代,只需要更换3D模型即可,缩短了研制周期。四是减重,结构优化让重量减轻。
这四方面对航空发动机的研制企业有巨大的诱惑力。GE、罗罗等航空发动机企业非常重视这项技术的研究,在一体化、轻量化、精密复杂、大型薄壁结构研制上得到有效应用。此外,3D打印在发动机零件修复方面潜力巨大。在应用途径上,一些制造成本高,尺寸精度要求比较高的零件修复,3D打印变形程度远小于熔焊变形,在整体叶盘、机匣、叶片等复杂零件修复上有巨大优势。在航空发动机修理和再制造上有巨大的应用前景。
3D打印航空发动机应用存在的问题与挑战
第一,技术要求不均,主要是靠供货商和采购方协商解决,各个工厂之间技术要求差别比较大。第二,增材制造粉末工艺检测全链条基础实验还不充分,无损检测、复杂曲面、晶格结构如何检测,内腔内流道表面质量如何控制等方面应用还需要更进一步细致的工作。第三,增材制造件可靠性的认证。目前增材制造的标准参考了锻铸件的标准,基本满足适航体系的要求,还需要进一步的研究,一个新零件通过3D打印用到航空发动机上,需要零件稳定性的验证、工艺平台的建立、工艺参数的优化、热处理组织性能的研究、表面处理、批次性考核、力学性能的验证、疲劳性能实验、工艺评审、建立相应的体系性的标准,通过试车考核以后才能应用,应用验证的路途漫漫。第四,降低增材制造的成本,缩短研制周期。目前在预研和研制初期,增材制造成本和周期方面有优势,但随着批量的上升,进入批产和维修期以后进一步降低增材制造的成本,缩短研制周期和制造周期是一大难点。
应用前景和展望
基于增材制造工艺约束的设计概念要贯穿始终,包括一体化、轻量化的设计,提升发动机性能。减少工艺辅助的结构,降低后处理的难度、几何复杂性、制造复杂性零件成本,这些都是在设计阶段要考虑的问题。
增材制造仿真技术的应用,可以减少前期研究的工作量。通过仿真技术的研究,解决残余应力和变形预测问题,缺陷预测和微观组织演变问题,工艺设计阶段支撑优化问题,通过模拟仿真提供理论参考依据,包括成型过程中的应力和变形,甚至开裂缺陷的预测。
增材制造技术与传统技术的集成。例如,机匣零件分布了很多凸台,按照传统方法制造厚度就非常大,加工周期大概需要十天,如果应用复合制造的方法,在锻件技术上加增材制造,也可以在铸件的基础上增加增材制造。增材制造与传统工艺结合,解决新品加工和零件修复过程中的成本、周期问题。
进一步扩展增材制造在航空发动机上的应用。结合国外的应用案例,分析增材制造技术的特点,确立航空发动机重点应用的典型零件,通过仿真技术、粉末制备技术、收缩变形、支撑等关键问题的突破,建立数据库,建立3D打印制造流程标准体系,从而在航空发动机应用上进行全面的推广应用。(中国航发)